3、典型案例分析
3.1案例简介
某大型光伏材料生产加工企业,主要以生产单晶硅、多晶硅为主,生产设备以直拉炉为主。变压器共计30台,携带直拉炉共计487台,其中19台2500KVA变压器各携带19台直拉炉,共计361台直拉炉;8台2000KVA 变压器各携带15台直拉炉,共计120台直拉炉;3台1600KVA 变压器各携带12台直拉炉,共计36台直拉炉。每台变压器正常工作时,负载率大于85%。项目已投入运行1年左右。
3.2存在的问题或隐患
经与客户方沟通及现场考察情况来看,存在下列问题:
①部分用电设备经常无故出现故障。经测试,谐波电压畸变率高达8.5%,谐波电流畸变率高达29%,电能质量情况非常恶劣。
②各工艺环节设备数据采用人工管理。能耗较大,但缺乏科学依据,所以节能无从下手。
③工艺设备故障不能及时维护。
④设备管理缺乏系统的信息化管理方式。
3.3解决方案
根据客户现场的实际工况,我们从四个方面着手进行解决:
第一,电能质量治理。在各变压器低压侧配置相应容量的有源电力滤波器,进行谐波集中治理,使配电网更安全稳定。
第二,电能监测及工艺设备数据管理。实时监测配网电能质量及设备的实时运行参数等数据,自动存储、分析,可生成相应的报表供管理者随时调看,作为后续节能管理的科学依据。
第三,信息发布。能够将设备的重要参数、能耗或故障等信息及时发送至相关责任人的手机、邮箱或者指定的FTP服务器等终端,让相关责任人能及时处理相关事宜。
第四,设备集中统一管理。各设备进行科学集中调度,使得各设备能够有机协调工作,在确保配电网安全稳定的前提下,最大程度的提高生产效率及能源的使用效率。
3.4运行效果
谐波治理,通过有源电力滤波器的统一控制,电能质量情况有了很大改善,治理后所有指标均满足了国标的要求,如图8所示,从而有效保障了配电网的安全稳定运行。
提高设备的使用效率,通过智能配电电能质量综合管理系统上线运行,现场工况得到了很大的改善。譬如设备工艺数据的管理,经工艺设备管理软件系统的排产优化分析,根据整个工艺周期的能耗统计曲线,以单晶硅直拉炉工艺周期为例,如图9所示,峰值时有功约为156kW,平均值为93kW,约为峰值功率的60%,依据“削峰填谷”的原理,协调各设备的运行工序,最终提升了30%左右的配电带载能力,使得电能的使用效率得到了极大的提高。
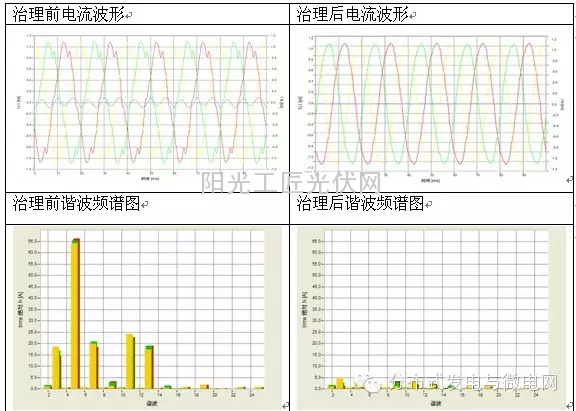
图8 电能质量治理前后对比
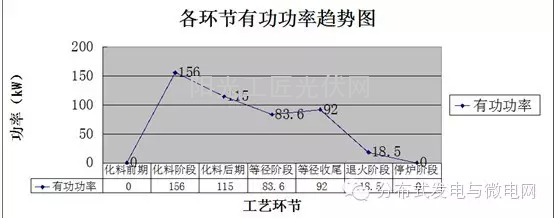
图9 各工艺环节有功模板图
4、结语
今年以来,光伏材料加工产业,如多晶硅加工等,已经呈现出回暖复苏的趋势,市场的需求量也在逐渐增加,这就促进了产业的新一轮投入发展。光伏产业在如火如荼发展的同时,势必带来了另外的一些问题,诸如光伏企业配网电能质量问题,生产各工艺环节能耗问题及生产设备维护及时性等问题。
而智能配电电能质量综合管理系统,正是从光伏企业的配网安全、电能监测及能效管理等角度,统筹兼顾,不断帮助客户提高配电网的安全稳定性及能源使用效率,真正把光伏产业建设成为绿色环保产业,实现全行业健康和可持续发展。