1、TOPCon技术:TOPCon采用背面氧化层+掺杂多晶硅的复合结构,形成良好的钝化接触,全面提升电池的性能。
2、TOPCon工艺流程:
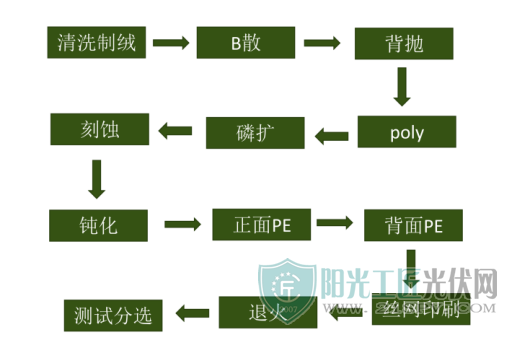
4、PE和LP:PE路线有先天性问题,体现不出TOPCon的优势。Poly沉积快,致密性很差, 用PE做的电池效率低。从量产角度看,LP已经满足需求,后续LP将是主流。
5、N型和P型技术路径和难度对比:P型做TOPCon容易很多,但效率提升不太明显,仅比P型PERC效率高0.5pct左右。这主要是载流子的问题,P型的载流子是空穴,跃迁相对比较难,而N型的载流子是电子,所以目前主流选择N型。
6、TOPCon和IBC结合的可行性:今年除了是TOPCon的元年,也是N型硅片的元年。N型硅片具有先天性优势,TOPCon技术是可以和HJT和IBC技术融合的,但是目前TOPCon尚且处于能做的阶段,而不是技术很好的阶段。
二、TOPCon与PERC对比
1、优势:
效率高:TOPCon目前量产效率最高的厂家效率高达24.8%,当前主流的PERC是23.2%,TOPCon高1.6个百分点。预计到2023年下半年,TOPCon可以达到 26.8%,PERC的效率在23.5%左右,效率差能达到3.3个百分点。
衰减低:一方面,TOPCon电池没有掉档的情况,而PERC电池目前的测试效率经一段时间后复测效率掉1~2个档;另一方面,对于组件端,TOPCon发电功率不存在衰减,PERC首年有接近8%的功率衰减。
长波响应好:PERC只是对短波响应好,TOPCon不管是长波还是短波响应都很好。TOPCon不受天气影响,发电量持续保障,而PERC发电量受天气影响严重。
2、劣势:
固定投资高:TOPCon设备投资2亿元/GW,而PERC是1.2亿元/GW。
工艺复杂:TOPCon工艺是12步,而PERC是11步,TOPCon新增三道工序,删掉了两道工 序,调整了一道工序,但它新增的几道工序都是比较复杂难以控制的。
非硅成本高:目前来看TOPCon非硅成本是0.26-0.27元/W,PERC是在0.2元/W 左右,TOPCon比PERC高30%,预期最终两者成本均有所降低后TOPCon成本比PERC高20%。
三、TOPCon与HJT对比
1、优势:
技术成熟,兼容性好:TOPCon的技术相对成熟,兼容性好,12道工序中有8道工序和PERC完全一样,新增的三道工序里面,设计的操作、工艺窗口、参数设置等与原有的PERC近似度非常高。
车间投资低:TOPCon设备投资2亿元/GW,而HJT目前来看要做到3~3.5亿元/GW。
量产性好:TOPCon的操作员工和工艺设备都可以直接从PERC原有车间无缝衔接,不需要做额外培训和技能升级。
效率高:目前TOPCon比HJT效率高0.4pct,预计到2023年效率差可能还会拉大。
非硅成本低:TOPCon是0.26-0.27元,而HJT目前是0.33元。
电池无衰减:TOPCon不管是电池端还是组件都没有衰减,但是HJT因为使用低温凝胶,效率逐渐衰减。
2、劣势:
工艺流程长:TOPCon有12步,而HJT只有5步(清洗制绒、掺杂晶体硅、导电膜、丝网印刷、测试分选)。工序流程越长,意味着设备对应的人员、工艺复杂度等增加很多。
车间占用面积大:工艺流程长造成需要的设备多,土地占用面积大,同时整个工程车间的设备动力成本等也会相应增加。
硅片厚度降低幅度小:PERC的硅片厚度在170~175μm之间(如果减薄太多,铝背厂的应力将导致硅片强度不达标),TOPCon目前主流能做到150~155μm(要面临硼扩的超高温和剧烈升降温的考验,后续应该不会减薄太多),HJT目前主流的实验室批量在110~120μm之间,有极个别的厂家能做到90μm左右。TOPCon省了约20μm左右的厚度,而HJT省60μm左右。
硅片尺寸受限:TOPCon尺寸目前主流是182,210目前来看阻力较大,主要的阻力来自于电池板和组件端的面积。而HJT受工艺的限制小,可以优先上210尺寸。
3、HJT量产化遇到的问题:
低温银浆:250度的超级低温导致银浆的金属化非常差,带来很多的衍生问题,最大的一点在于组件的焊接拉力完全不达标。
TCO膜:TCO膜特别容易老化,老化后性能下降很严重。PERC和TOPCon电池组件寿命一般 是15~20年,而HJT技术在实验室恶劣条件下,TCO膜的寿命是3~5年。
PVD&RPD设备:设备来源于半导体,要精准控制,但是它连续作业能力不高。
原标题:TOPCon电池与HJT&PERC电池优劣点