
同时,基于市场不同场景、不同客户类型的应用需求,未势能源IV型储氢瓶全系产品规划已在同步推进中,工作压力覆盖35MPa和70MPa,包括 70MPa-23L、35MPa-210L等不同规格型号的产品序列,部分商用车载IV型储氢瓶质量储氢密度指标可达到6.8wt%,且全系产品均已实现关键核心技术100%自主可控,关键原材料(如碳纤维)与核心配套部件(如瓶口阀、内胆等)实现100%国产化,综合成本降低20%,且具备轻量化、长寿命、高安全等综合性能优势,并将于近期陆续发布,可提供定制化产品开发,广泛适用于燃料电池乘用车、商用车(重型卡车、公交客车、冷链物流车)、船舶等多种场景及领域。
在IV型储氢瓶的开发过程中,未势能源基于客户端不同工况环境应用需求,结合氢气介质的特殊性与储氢系统功能、结构等匹配特性,充分发挥储氢领域关键技术研发优势,通过大量的可行性设计方案和试验验证,聚焦“新材料、新技术、新工艺”的应用,陆续攻克IV型储氢瓶多项关键技术难题。
攻关新材料开发 从源头摆脱应用局限
未势能源聚焦关键材料的开发与应用,联合国内多家知名高校、科研院所、供应链伙伴等共同开展深度合作,重点针对塑料内胆原材料的氢阻隔性,内胆在泄放过程中容易产生的鼓包、屈曲、塌陷,航天级铝合金的化学成分控制、热处理状态,碳纤维预浸带的加工及配套树脂的性能等共性技术“卡脖子”难题,逐层进行技术攻坚,从源头摆脱核心材料进口、高昂成本带来的应用局限。
目前,已陆续取得了包括内胆高分子原材料选型,高强度新型纤维预浸带与配套树脂配方等关键共性技术研发和应用验证,从源头上为储氢气瓶的力学优异性能、质量稳定性与国产化替代提供重要保障,具有重要的科学意义和工程应用价值。
创新结构设计 提升产品可靠性
新材料的选择固然重要,但要真正体现储氢瓶质量稳定性、一致性与适用性水平,必然离不开科学的结构设计。

瓶口部位金属阀座与阀门的转接头结构,摒弃常规繁杂的多部件结构设计,通过自主创新内胆、阀座密封结构与界面化设计,实现一体化“直连”。其中,金属阀座采用轻量化结构设计,外观曲线与内胆封头曲线光滑连接,充分考虑外界冲击时阀座与碳纤维复合材料的相互作用,做到防滑、防转,并配合有限元分析软件,在科学的安全系数下做到极致“轻量化”设计,重量较竞品减轻40%,并创新高性能“密封”解决方案,降低了氢气泄漏、渗透隐患,进一步提升了产品的安全性。
另外,在碳纤维铺层设计方面,通过采用遗传算法、仿真模拟软件等科学设计方法,优化缠绕角度及铺层顺序,将碳纤维预浸带的纤维强度、韧性发挥到最大化,确保储氢瓶在氢燃料电池汽车整个生命运营周期的抗压性与可靠性。
革新“干法缠绕”工艺 助力行业降本增效
基于新材料选型与新结构设计,未势能源大胆创新全流程生产工艺设计,在内胆成型技术方面,采用目前国内较少应用的注塑-焊接工艺,使得内胆厚度均匀性、尺寸稳定性达到行业较高水准。
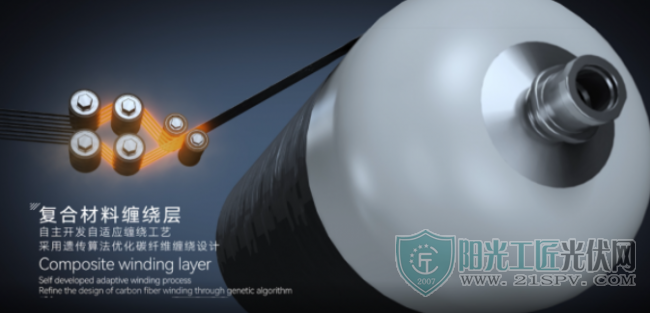
同时,首创性的采用预浸带“干法”缠绕工艺,产品性能指标的离散系数可控制在2-3%,缠绕效率较湿法提高80%以上,固化时间缩短30%,疲劳测试寿命>44000次,在达到轻量化目标的同时,进一步确保碳纤维强度的发挥率、爆破强度和压力循环寿命一致性,有效解决内胆褶皱、屈曲等关键问题,大幅提升质量储氢密度、生产效率与质量,且缠绕过程无滴胶、漏胶等现象,生产环境更加友好,为后续规模化量产与市场供应,提供了有效的数据支撑与运营经验。
目前,未势能源自主开发的第二代IV型储氢瓶系列,已陆续完成火烧试验、耐久性试验、使用性能试验等多个关键试验项目测试,生产线建设已进入尾声,“三新”评审相关工作正在有序推动中。
这也是未势能源聚焦氢能储运领域,以“卡脖子”技术为突破口,继70MPa储氢阀门产品之后取得的又一重大科研创新成果,标志着未势能源在储氢技术领域,从产品开发到应用,已具备成套储氢系统关键技术及核心部件设计、开发与制造能力,并将有助于未势能源拓展产业链供应端与应用端布局,进一步满足正在增长的高压氢气储运市场需求,为行业客户提供更专业、更优质、更具高性价比的解决方案,切实助推氢能储氢装备加速国产化替代,打开降本增效新空间。
原标题: 国际领先!未势能源IV型储氢瓶质量储氢密度突破6.1wt%