1.0绪论
电池片作为光伏组件重要原材料之一,在组件系统应用中起着十分重要的作用。由于硅材料的紧缺结生产成本的降低,电池片厚度由2005年的220-270μm减到目前的170-190μm,其发展趋势还有可能更薄。因此,如何应对电池片裂纹、破片所带来的制作成本的增加,如何避免组件层压前制作工序中电池片产生的裂纹、破片和层压后各工序中的周转造成组件挠曲是电池片产生隐裂或裂纹,以及如何解决系统应用中出现不良问题的索赔等,是目前组件厂商值得探讨和思考、且迫在眉睫需要解决的问题。
图1是各工序破片比例图,此柱状图可直观反映各工序的破片率情况。
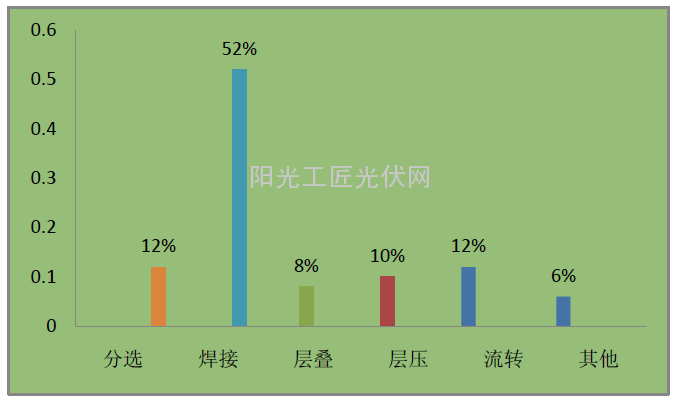
图1各工序破片比例图
2.0电池片分选工序中裂纹、裂片的原因分析
在分选过程中,容易造成裂纹、破片的环节有:拆封电池片、测试电池片、电池片堆放和流转等,现就这三个环节分析器原因及提出正确的解决办法。
1.拆封电池片
来料电池片都是用热塑薄膜包装好的,所以拆封电池片的方式很重要,若拆封方式不正确,容易造成电池片破碎、缺胶等现象。不正确的拆封方式见图2,正确的拆封方式见图3.
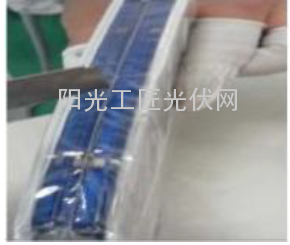
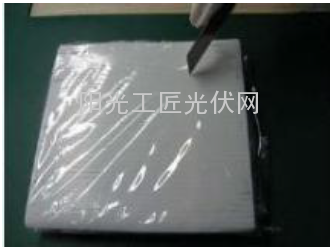
图2 不正确的拆包方式 图3 正确额拆包方式
2.电池片堆放和流转
在电池片堆放和流转的过程中,若方式不当,易造成裂纹。图4为不正确的堆放方式,图7为正确的堆放方式。
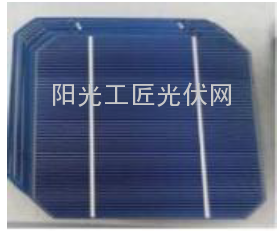

图4 堆放不当易造成破片、缺角 图5做好缓冲,减少破片
3.0焊接工序中裂纹、破片的原因分析
在焊接过程中,容易造成裂纹、破片的环节有:电池片焊接工艺、互联条的选择、焊接后的堆放等,现就这三个环节分析器原因及提出正确的解决办法。
1.电池片焊接工艺
(1).烙铁气筒的温度太高容易造成电池片起头焊接时成八字形隐形的裂纹,这种现象一般很难发现,建议定时检测烙铁温度,焊接时操作员工及时反馈焊接效果,并仔细检查焊接好的电池片,减少这种隐形裂纹流转入下一道工序的几率。选择合适的焊接温度既能保证焊接质量又能减少破片。
(2)焊接时有堆锡的现象,在串焊层压工序也将造成电池片裂纹、破片,建议合理调整员工的焊接手势,减少堆锡的现象。
(3)串焊是如果焊接起点和单焊的起点重合,则容易造成电池片裂纹或者破片。
组件在户外使用过程中,承受热胀冷缩会使原本有裂纹的电池片裂纹逐渐变大,从部分电流的损失直至整片电池片完全无电流产生。